www.mexicoindustrial.net
02
'19
Written on Modified on
Lo primero es la seguridad
Para que las personas y los robots puedan trabajar en armonía en las áreas de maquinado comunes sin ninguna barrera protectora de separación, han de cumplirse requisitos de seguridad estrictos.
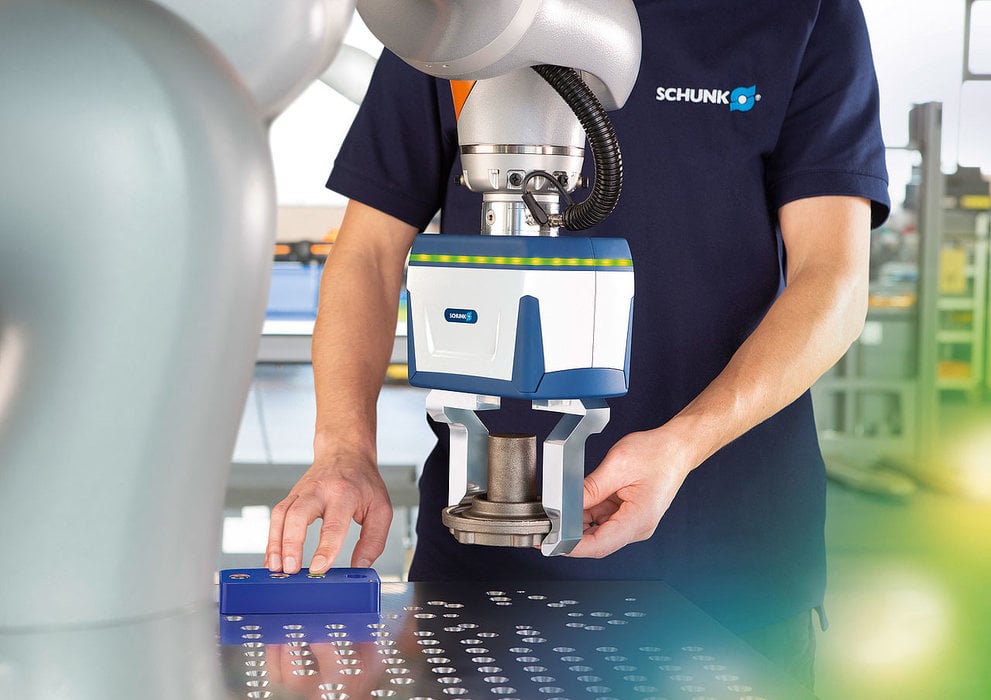
Como fabricante de componentes de sistemas de agarre con certificación HRC, SCHUNK adoptó la decisión consciente de tener en cuenta los aspectos relacionados con la seguridad en el trabajo al inicio del proceso.
De este modo, tales aspectos se incorporan en los nuevos sistemas de agarre desde el principio.
Esto acorta el proceso de desarrollo con componentes estándar, reduce los costes y acelera los proyectos de colaboración entre humanos y robots para aplicaciones específicas.
"La validación de las aplicaciones de colaboración entre humanos y robots plantea un reto particular", afirma el profesor Dr. Markus Glück, director ejecutivo de Investigación y Desarrollo de SCHUNK.
Del lado del usuario, ha habido muchas dudas sobre cómo aplicar realmente en las directrices y normas los requisitos de seguridad y de salud en el trabajo.
"Para que las personas y los robots puedan colaborar de forma segura, no solo se necesita un conocimiento profundo de la aplicación robótica, sino también un conocimiento especializado de la evaluación de riesgos", señala Glück.
Debido a que cada aplicación HRC es diferente, se requiere realizar una evaluación de riesgos individualizada en cada momento.
"La fuerza, la velocidad y las trayectorias de desplazamiento del robot y de la pieza en particular, incluido el portapiezas, representan peligros para el trabajador."
"Estos deben limitarse mediante el uso de medidas de protección inherentes o, si es necesario, mediante el uso de medidas adicionales de protección frente a riesgos", subraya el profesor Dr. Glück.
"Nuestro objetivo es dotar a los fabricantes de robots, integradores y creadores de sistemas de componentes maduros probados de forma independiente que puedan utilizar para crear escenarios de colaboración de forma más rápida y certificarlos."
Serie Co-act certificada
La serie Co-act EGP-C certificada para aplicaciones de colaboración demuestra su aspecto real. La cartera de pinzas comprende cuatro tamaños, está diseñada para tareas de manipulación sencilla y puede instalarse de forma intuitiva en casi todos los robots ligeros comunes como una solución Plug & Work.
"Con más de 400 instalaciones de productos actualmente en curso en clientes y socios, Co-act EGP-C ha demostrado de manera contundente su madurez", destaca Markus Glück.
La fuerza de agarre que ejerce sobre el dedo, que tiene un diseño inherentemente seguro, está limitada a un máximo de 140 N por motivos de seguridad.
Los módulos de programación de alto rendimiento y los complementos simplifican la instalación.
Los dedos de acoplamiento normalizados con elementos intercambiables de uso universal facilitan a los nuevos usuarios su entrada en el mundo de la robótica colaborativa.
"Cuando los humanos y los robots comparten un área de mecanizado, los bordes han de redondearse para que los primeros no se corten si la pinza les produce algún rasguño o ejerce una presión activa sobre ellos", destaca Glück.
"Del mismo modo, ha de evitarse el apisonamiento de los dedos y la piel." La visualización clara de la situación operativa actual a través de LED de colores también genera confianza.
Consulta durante el desarrollo del producto
Con Co-act EGL-C, SCHUNK va un paso más allá. Gracias a este potente equipo, ha sido posible por primera vez fabricar una pinza para aplicaciones de colaboración donde la fuerza de agarre que ejerce sobre el dedo supera el límite de 140 N considerado no perjudicial para la salud.
Al igual que con el gripper para componentes pequeños de SCHUNK Co-act EGP-C, SCHUNK ha dado también una gran importancia al Deutsche Gesetzliche Unfallversicherung (DGUV) que acompaña el proceso de creación del producto para la Co-act EGL-C.
Esta colaboración ha facilitado la comunicación desde el inicio del proceso y el control y respeto eficientes de las normas.
Además, ha sido posible adquirir experiencia acerca de la manera de poder diseñar la certificación y la evaluación de la seguridad para que sea fácil de usar, sin comprometer la calidad a la hora de tener en cuenta la seguridad.
"El concepto de seguridad de esta pinza es altamente sofisticado", expone el profesor Dr. Glück.
Añadió además que "Por medio de consultas oportunas durante el desarrollo de la pinza, fuimos capaces de garantizar que, en lo referente a la electrónica de seguridad, la técnica de control segura y el concepto de seguridad en su conjunto, se puso especial atención desde el principio al respeto de las normas y las reglamentaciones jurídicas pertinentes".
El agarre en tres fases
Un sistema de inteligencia de seguridad desarrollado por SCHUNK cuya patente se encuentra en curso de tramitación divide el proceso de agarre de la Co-act EGL-C en distintas fases.
Siempre que exista un peligro de apisonamiento de manos o dedos, el sistema integrado de inteligencia limita la fuerza de agarre a un umbral no perjudicial de 30 N.
Solo desde una distancia de la pieza de más de 4 mm, en la que no hay peligro de apisonamiento, los dedos prensores se aproximan con la fuerza de agarre de libre elección de hasta 450 N.
Si el sistema detecta flexibilidad en esta fase de cierre, por ejemplo porque la pieza que se agarre sea demasiado pequeña, y el operador desea retirarla manualmente, este movimiento se detendrá también automáticamente.
Lo mismo ocurre si el tamaño de la pieza se pasa 2 mm de las medidas anticipadas si, por ejemplo, no hay piezas disponibles.
En la tercera fase, la pinza finalmente detecta si la pieza se ha agarrado con seguridad y tensa el freno.
Como resultado, la EGL-C de SCHUNK satisface los requisitos de colaboración segura entre personas y robots y garantiza que las piezas agarradas, que en el agarre por arrastre de fuerza pueden pesar hasta 2,25 kg, tampoco se pierdan en caso de una situación de parada de emergencia y la correspondiente frenada a fondo. En el agarre por arrastre de forma pueden pesar incluso hasta 8 kg.
El concepto de seguridad modular como objetivo
Sin embargo, respecto a la certificación, aún quedan muchos deseos por cumplir: "Para que la colaboración entre humanos y robots alcance su pleno potencial, necesitamos una solución que permita que los integradores y los operadores creen sus propios procesos de colaboración con un esfuerzo razonable.
Incluida la validación de la seguridad y de la salud en el trabajo", subraya Glück.
Los conceptos de seguridad modular propuestos por SCHUNK y que pretende aplicar con sus pinzas certificadas pueden proporcionar a los usuarios una orientación y simplificar la validación de la seguridad y de la salud en el trabajo considerablemente en cada uno de los casos.
"Si los usuarios pudieran contar con componentes certificados en el diseño de una estación de trabajo de colaboración entre personas y robots, la introducción de esta colaboración en la producción diaria sería considerablemente más rápida", expone Glück.
En su opinión, el panorama normativo de HRC también seguirá desarrollándose con mayor profundidad.
Por ejemplo, ISO/TS 15066 ha de ser revisada como especificación técnica pasados cuatro años a más tardar.
"Por este motivo, es importante que los fabricantes de robots, los proveedores de herramientas de agarre y los integradores y efectores terminales cooperen de forma activa con los organismos de control como el DGUV para seguir perfeccionando las normas", afirma Glück.
"Los aspectos relacionados con la seguridad han de ser prioritarios en este caso y sin hacer ningún tipo de concesión. Al mismo tiempo, su aceptación será mayor cuando los temas de seguridad y simplificación puedan armonizarse durante la instalación y la certificación."
Normas y directrices relativas a la colaboración entre personas y robots
Los requisitos legales de los escenarios de colaboración se describen en un principio en el anexo 1 de la Directiva 2006/42/CE relativa a las máquinas: "El fabricante de una máquina, o su representante autorizado, deberá garantizar la realización de una evaluación de riesgos con el fin de determinar los requisitos de seguridad y de salud que se aplican a la máquina".
Para la evaluación de riesgos, el análisis debe incluir el entorno inmediato de las aplicaciones.
Se ha de proteger eficazmente toda posible colisión perjudicial, incluido el apisonamiento de extremidades, los guantes de trabajo o cualquier tropiezo del trabajador.
Al mismo tiempo, las referencias normativas relativas a la seguridad funcional de las aplicaciones HRC son normas generales como IEC 61508, IEC 62061 e ISO 13849-1 y 2.
Además, han de tenerse en cuenta las normas ISO 10218-1 y -2 para la seguridad de los robots industriales.
La especificación técnica ISO/TS 15066:2017-04 define en particular los principales requisitos de uso de los robots en las actividades de colaboración y dispositivos de robótica.
Esta "norma HRC" describe las indicaciones de uso de cuatro tipos de colaboración y explica detalladamente los principios de seguridad necesarios.
También recoge las especificaciones detalladas sobre umbrales de dolor que han de respetarse en relación con las partes corporales pertinentes.
www.schunk.com