www.mexicoindustrial.net
20
'20
Written on Modified on
The Smart Factory – An Overview
The smart factory is still a work in progress, but the building blocks are already in place. A report.
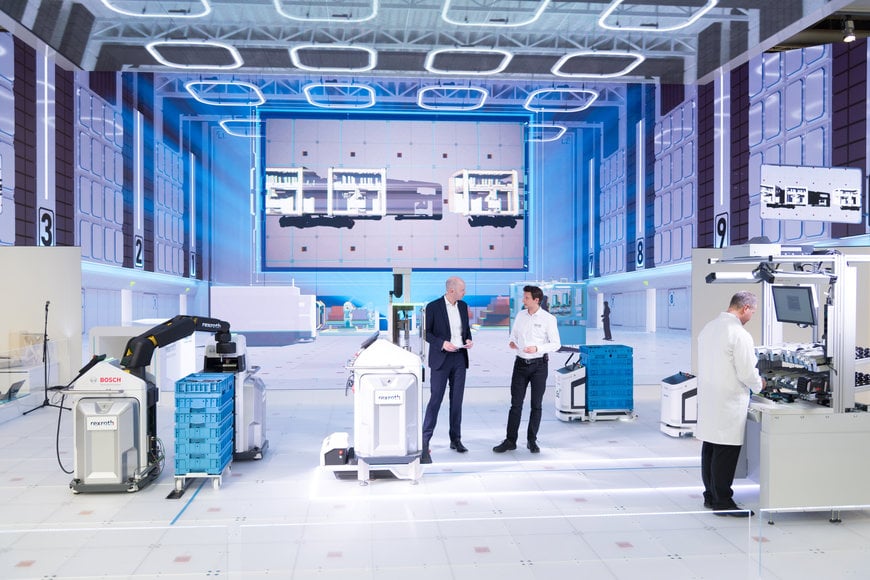
Autor: Milton D'SILVA
A couple of years ago, a technocrat from a leading automation vendor, chatting on the side-lines of an industry event made an interesting observation. “A factory manufactures products, but that is not the purpose of the factory,” he said. “The purpose of a factory is to make profits.” Implicit in this assertion is the role technology plays in making those profits. It started with the very first Industrial Revolution in the mid-18th century powered by steam, and continues with the Industry 4.0, the fourth version – unleashed by the Internet and facilitated by cyber physical systems in the new millennium.
Each of these revolutions brought in tremendous advantages in terms of transportation, telecommunications, access to raw materials, exploration of resources, etc., and led to large scale manufacturing of industrial and consumer goods, gadgets and appliances for everyday use. However, by now, most of these advantages have been exploited to the hilt, and production efficiency in some sectors has reached in the higher 90s in terms of percentage. Yet today, more than at any other time in human history, manufacturers are under constant pressure to produce higher quality products in lesser time at lower prices, and to suit individual requirements as well. With margins shrinking, the only way to squeeze profits is to further increase efficiencies, reduce errors, anticipate failure of equipment and eliminate breakdown altogether.
Welcome to the Smart Factory era, made possible by the bouquet of emerging technologies now available to the industry in quest of still higher efficiencies.
What exactly is a Smart Factory?
In simple terms it is a place for smart manufacturing where machines, already automated to a great extent – and increasingly intelligent robots – are linked together by smart devices through the Industrial Internet of Things (IIoT). This in turn facilitates self-learning and adaption, improving the processes through advanced automation and self-optimisation, with seamless end-to-end connectivity and data analytics. The resultant benefits are not just in terms of efficient production, but also the streamlining of all related functions like supply chain logistics and pre- and post-production processes, to make it sustainable. The secret to unlocking this potential is hidden in the data generated by these processes. According to an IBM report, an average factory generates 1TB of production data each day, of which over 99% is not analysed. The information hidden in this data, the analysis of which is beyond human capabilities and needs technologies like artificial intelligence and machine learning, holds the key to greater operational efficiencies.
The smart factory does not necessarily have to be built from scratch. Existing facilities can be transformed into smart factories, provided there are investments made to put a few things in place. These include a proper network infrastructure, smart controllers, analytics software with integrated information systems including IoT, cloud computing, Big Data and technology using artificial intelligence. Above all, this needs skilled manpower and the preparedness to adapt to new technologies.
The smart factory is still a work in progress, but the building blocks are already in place. However, there are gaps to be filled – while Artificial Intelligence plays a key role in data analytics, 5G is the go to technology for connectivity – and a lot remains to be done in both these areas.
So what is the status of the smart factory and its implementation from the perspective of the leading vendors of technologies for the smart factory? Presented here is a snapshot of 5 leading vendors and their technologies.
ABB and its Ability
A custom-made wristwatch assembled within three minutes. That is what ABB demonstrated at Hannover Messe 2019 at the smart factory module on display at its booth, using three of its key technologies – the YuMi collaborative robot performing precision assembly operations; the SuperTrak flexible transport system ensuring timely movement of parts; and the ABB Ability Connected Services monitoring health and performance. ABB launched the Ability technology platform in 2017, bringing together a number of its digital products, solutions and services under one umbrella. The ABB Ability platform today offers more than 220 digital solutions, which enable enterprises to increase productivity and improve safety at lower costs.
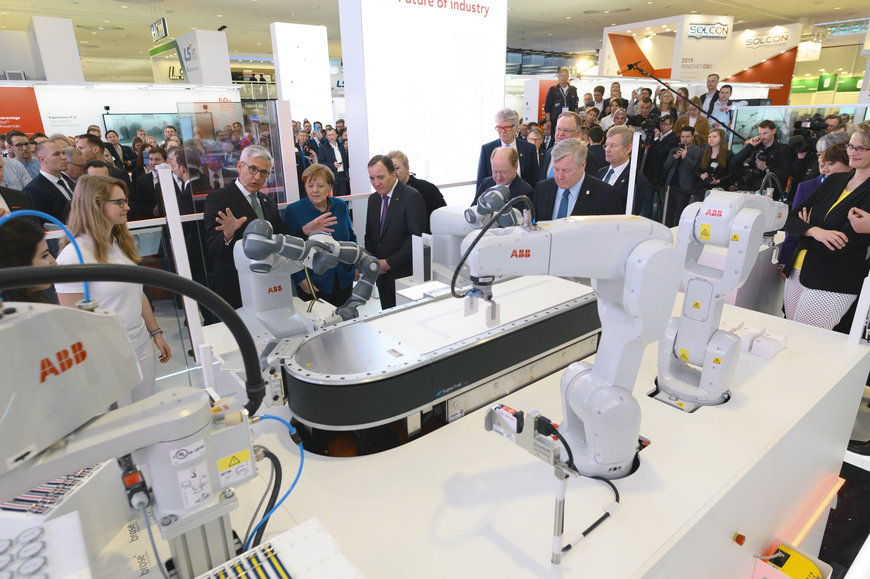
ABB’s smart factory module demonstrated at Hannover Messe 2019. Picture: Hannover Messe
The ABB factory at Heidelberg in Germany is a classic example of a smart factory, a showcase of ABB’s cutting edge technology as well as manufacturing prowess. One of the oldest plants of the ABB group, it manufactures miniature circuit breakers (MCBs), a common but critical safety device used in electrical installations, available in many different variants. The MCB effectively breaks the circuit in case of overload and other faults, protecting the installation from fire and damage. The Heidelberg plant is a demonstrator for smart manufacturing – of how the factory of tomorrow looks like. It is equipped with seven types of ABB robots, all interconnected on the ABB Ability platform, the digitalisation increasing their productivity. The transformation has increased the plant efficiency to handle 3 times as many product variants as before, adding to a whopping 6000 variants now, also improving quality of the products. Predictive maintenance practices have led to accurate delivery schedules and better in-plant material handling.
The Ability platform leverages intelligence gathered from ABB’s vast global installed base of over 70 million connected devices and 70,000 control systems. This not only helps customers optimise operations, but ABB also uses the insights to develop new business models.
Bosch goes beyond Mobility
Bosch, the renowned provider of vehicle technologies and mobility solutions, now offers Industry 4.0 technologies for smart factories. With the focus on automation, digitalisation, AI and IoT, the idea is to boost productivity, quality and safety. As a leading user and provider of Industry 4.0 solutions, Bosch follows the ‘3S’ strategy – using sensors, software and services. These are channelised through its software platform Nexeed, on which reside a variety of ‘Source-Make-Deliver’ solutions for continuous optimisation – from procurement (source) through production (make) to the end customer (deliver). Nexeed includes tools like predictive maintenance, cockpit charts, traceability and tracking solutions, manufacturing execution, maintenance support, autonomous transport systems, intralogistics – all connected. Nexeed is ideal for larger enterprises that have deployed Industry 4.0 solutions, companies that have global production network and plants at multiple locations. But Bosch also offers solutions to SMEs in smaller packages, introducing to them the benefits of Industry 4.0, especially when they do not have in-house digital expertise.
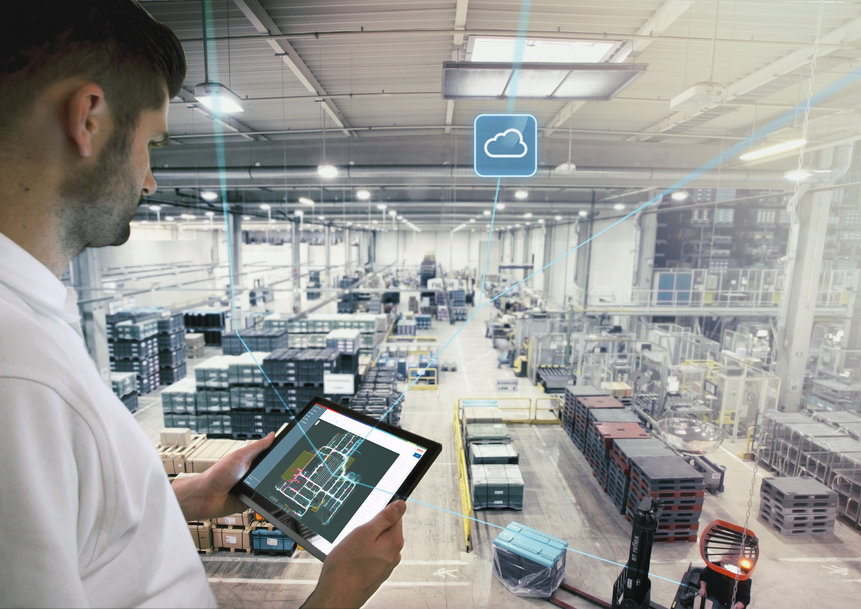
Bosch’s Blaichach plant in Germany, specialised in manufacturing ABS and ESP systems for automobiles, is a smart factory working on the Nexeed platform. This brings all the benefits of the connected plant for both new and existing machinery, as Nexeed is an open system, where it is easy to retrofit IoT devices on legacy production lines. The Blaichach plant employs 3000 associates as Bosch calls them, and produce 6.7 million ABS/ESP safety systems. The transformation has made it possible for Bosch to increase productivity at its ABS/ESP manufacturing facilities worldwide by almost 24 per cent.
For Bosch, these initiatives of integrating Industry 4.0 technologies in the smart factory is paying off with the company having earned more than Euro 1.5 billion with Industry 4.0 applications in the last 5 years. By 2022, Bosch has ambitious plans to generate annual sales of over a billion euros with Industry 4.0.
Rockwell Automation and The Connected Enterprise
Rockwell Automation believes the world needs to become a smarter place and offers solutions to that end through The Connected Enterprise, where products become smarter, people become smarter, and their decisions become smarter. The 117-year old company is a major provider of industrial automation and information technology products with global sales of USD 6.69 bn for 2019. The company conducts signature events like the annual Automation Fair in the US and the region specific TechED events at other global locations to connect with and educate customers about the latest developments in the field.
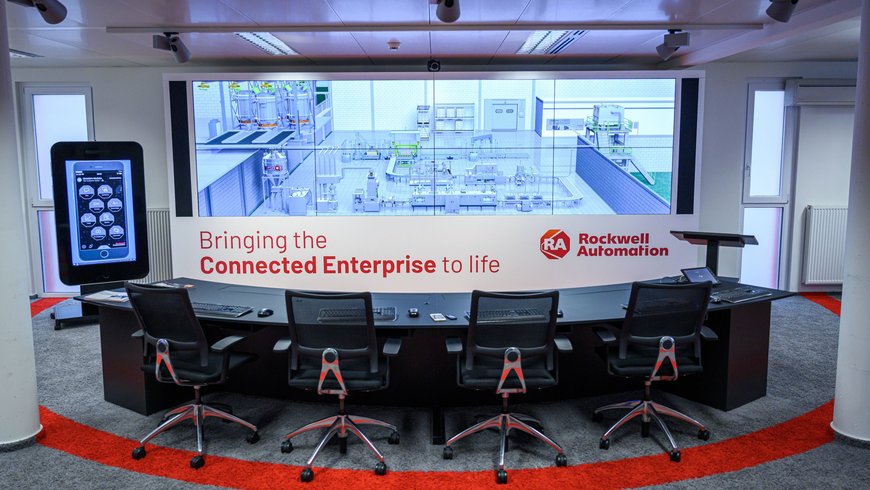
The Rockwell Automation EMEA Customer Center at Karlsruhe, Germany. Picture: Rockwell Automation
The hardware offering of Rockwell Automation comprises thousands of Allen-Bradley products, the software comprises numerous software suites under the FactoryTalk banner. The Connected Enterprise is a platform that brings these smart solutions together for the benefit of discrete manufacturing as well as process industries, bringing them tangible benefits like faster time to market for manufactured products, improved asset utilisation, lower total cost of ownership, and more effective enterprise risk management. That these are all tried and tested solutions is borne out by the fact that Rockwell Automation uses them in its own manufacturing facilities as part of its digitalisation transformation journey.
The Connected Enterprise, according to the company, is a five-step journey: identify a desired business outcome; get an outside perspective; assemble the team; implement a pilot program; and scale for expansion. For companies who adopt the platform for their digital transformation, the outcome, based on use cases, leads to: productivity increases of 4-5% per year; waste reductions that result in hundreds of thousands of dollars in savings; faster time to market, which includes plants that become operational in weeks instead of months; quality improvements that result in defects being cut in half; and up to 98% on-time delivery.
In 2017, Rockwell Automation opened its EMEA Customer Center for The Connected Enterprise in Karlsruhe, Germany, offering customers and visitors the opportunity to receive tailored advice on smart factory subjects combined with a 360-degree view of The Connected Enterprise.
Schneider Electric builds the EcoStruxure
Schneider Electric, the leader in the digital transformation of energy management and automation, traces its origins to 1836. It is a European multinational company with operations in over 100 countries and 2019 revenue of Euro 27 billion. Since 1980, the company has grown phenomenally through a series of acquisitions, shedding its traditional steel business in favour of electricity and related technologies.
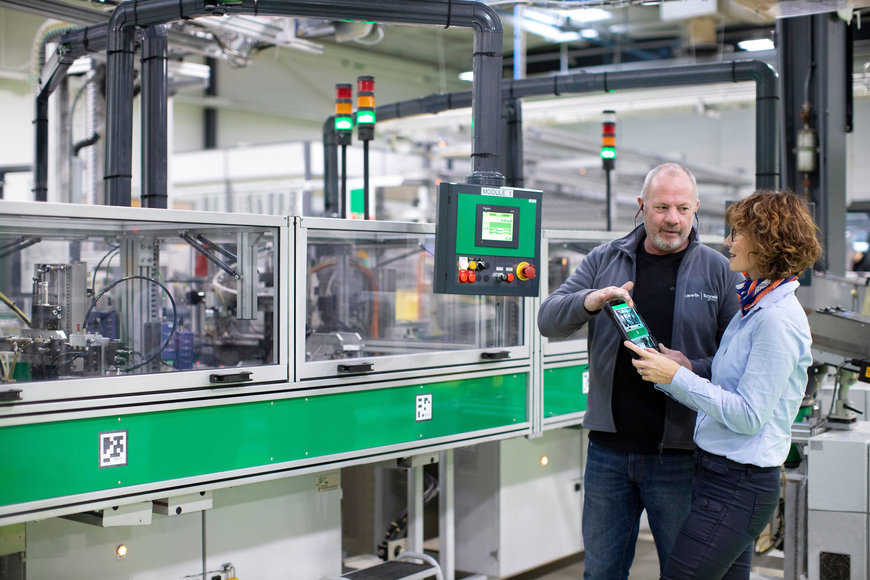
Having reinvented itself for the digital era in the new millennium, the company launched its IoT enabled EcoStruxure platform for digital transformation, with sector specific suites covering not just industries, but also homes, buildings, data centres, energy and infrastructure.
EcoStruxure for Industry is the Schneider Electric IIoT platform that is open, interoperable, and ready for smart manufacturing, at every level from Connected Products to Edge Control and Apps, Analytics and Services. It is the digital backbone connecting best-in-class operational technology (OT) solutions with the latest in IT technology to unlock trapped value in operations and leverage the true potential of the Internet of Things. With integrated software, it improves productivity, efficiency, sustainability, and cybersecurity for plants and machine builders. Benefits include up to 80% reduction in engineering costs and time; up to 75% savings in maintenance cost; and up to 50% reduction in carbon footprint.
Schneider Electric executives often say ‘we eat our own food’, which means the smart technologies the company offers to the industry are implemented in its own plants first. The company has launched several Smart Factories around the globe in countries like France, USA, Mexico, China, India, Indonesia, and the Philippines. These are central to its Tailored Sustainable Connected 4.0 supply chain digital transformation where it leverages digitisation across its supply chain operations to deliver end-to-end integration and visibility to enhance its performance. The World Economic Forum has designated the Schneider Electric facilities in Le Vaudreuil in France, and Batam in Indonesia, as Advanced 4th Industrial Revolution (4IR) Lighthouses. The company has set for itself a target of 100 smart factories for 2020, and the same technologies are available for any company looking for similar transformation.
Siemens and its MindSphere
Established in 1847, Siemens is the German multinational corporation and the largest industrial manufacturing company in Europe with a global footprint, with 2019 revenue of around Euro 87 billion. With its main business verticals of Industry, Energy, Healthcare and Infrastructure, Siemens today has the domain expertise and digital knowhow to generate performance improvements across the entire value chain through digital transformation. This is achieved with its two main solutions: MindSphere – a cloud-based, open IoT operating system; and Digital Twin – the virtual representation of products and production. Launched in 2016, MindSphere today connects an estimated 1.3 million devices and more than 1,000 customers. Global automobile giant Volkswagen uses MindSphere in its cloud network, connecting machinery and equipment at more than 120 of its plants. This data is used to improve productivity and efficiency across plants and production lines. What MindSphere does essentially are 4 things: connect assets and upload data to the cloud; collect, monitor, and analyse data in real-time; gain insights that improve efficiency and profitability; and take advantage of apps and solutions that solve real problems.
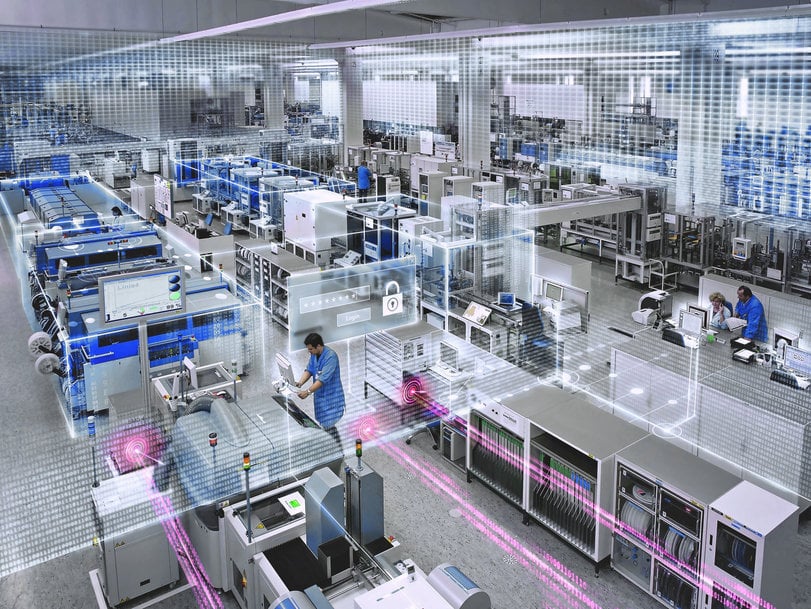
The Siemens Smart Factory at Amberg, Bavaria. Picture: Siemens
Like other major vendors, Siemens too has an excellent example of the Smart Factory in its Amberg plant in Bavaria, which has deployed the MindSphere system as well as executed the digital twin. Spread over 100,000 sq.ft, the Amberg plant manufactures a mix of 1200 products, which means on an average there are 350 production changeovers per day! The plant produces 17 million Simatic components per year, and about 50 million items of process and product data is evaluated and used for optimisation! In the process of the smooth running of the plant, Siemens uses other ground breaking technologies like artificial intelligence, machine learning and Industrial Edge computing. The results of the transformation are evident in the figures – a 13-fold rise in production since the plant started operations in 1989, without any additional manpower or expansion.
Summing up
According to a market research report on global smart factory industry posted by Reportlinker recently, the global market for Smart Factory is estimated at US$136.4 billion in the year 2020. This is projected to reach a revised size of US$218.4 billion by 2027. The expected additional value for manufacturing industry due to productivity gains in smart factories by 2023 is expected to be between US$1.5 to 2.2 trillion, according to the Capgemini Research Institute’s estimates, published in its report ‘Smart factories @ scale’. This indicates the potential gains of smart factory for the manufacturing world.
An important question that rises from these developments is the human role in the factory of the future with the spectre of massive unemployment caused by digitalisation. But Prof Martin Ruskowski, Chairman of the Executive Board at SmartFactory-KL, the manufacturer-independent demonstrator and research platform based in Germany, does not agree. According to him, “Humans will and must be able to change every decision made by a machine. We will retain responsibility for what happens in the production processes. Machines and artificial intelligence cannot and should not take this away!”