www.mexicoindustrial.net
09
'19
Written on Modified on
Siemens Mobility construye 73 tranvías para Múnich
Stadtwerke München (SWM) ha realizado un pedido adicional a Siemens Mobility de 73 tranvías Avenio más por valor de más de 200 millones de euros. Por lo tanto, la empresa municipal está dibujando las opciones existentes. Los tranvías complementarán los del mismo tipo ya en servicio en la ciudad. La entrega de los primeros vehículos está prevista para 2021.
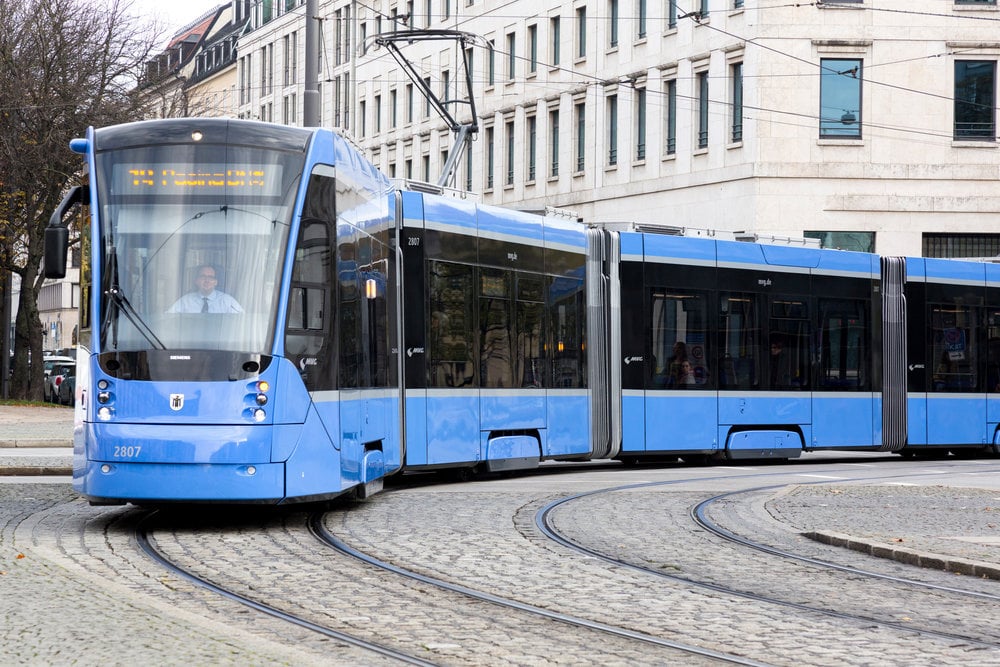
- Complete machining of complex parts - milling, drilling, turning operations in a single setup
- Expansion of capacities for complete machining
- High dimensional repeatability
- Best cost/benefit relationship
Complete machining of medical technology components
One area of focus is on the production of medical technology components. For instance, this includes the production of several thousand artificial knee joints annually. „These high-value, turned and milled components are subject to very tight tolerances and must still be produced profitably“, insists Eng. Erwin Poinstingl. Consequently, these parts must be produced in a complete machining center, which is able to perform milling, drilling and turning operations in a single setup.
Encouraged by the success and demand in this field, MKE has decided to invest in a new 9 axes machine. This machine is expected to complement the existing turning/milling machine, but also to significantly expand the capacities for complete machining. As part of their research for the correct concept, the MKE managers also turned to EMCO Maier GmbH. „We have had ties to EMCO for 15 years, which are rooted in trust and effective collaboration“, Eng. Erwin Poinstingl reveals. For instance, MKE has already been machining on two Hyperturn 665 MC and several teach-in lathes and milling machines. EMCO, in turn, has outsourced its bar-feeder production needs for the various turning machine models to MKE.
Hyperturn results in capacity expansion
MKE‘s attention is specifically directed toward the Hyperturn 95 SMB (HT 95) which is ideally matched to the product spectrum with its 95 mm bar capacity and corresponding level of automation. After a detailed technical review and comparison to models from other manufacturers, the company decided in favor of the HT 95. „EMCO machines are top-notch with respect to quality and are also priced well. This is complemented by exemplary and reliable service – these are key benefits“, the MKE Managing Director notes.
The company was specifically impressed by the rugged design and high dimensional repeatability. The HT 95, which is specialized on processing rods, uses the same machine frame as the HT 110, which is larger due to its specialization on flanged parts. „Machining processes are therefore very stable and vibration-free – a benefit that is also reflected in increased tool life“, explains Gerhard Meisl, Product Management Manager at EMCO.
The work space of the HT 95 provides very good accessibility to the individual components. Generously dimensioned access space provides for ideal chip flow, even when machining difficult materials. All machine ways are covered with stainless steel panels, in order to prevent damage. „With this machine size, we incorporate on main and counter spindle most modern integrated spindle motors with a spindle speed of up to 3500 rpm. These guarantee high positioning accuracies combined with high dynamics and the necessary contour milling precision for machining complex and accurate parts. The water cooled milling spindle with 12,000 rpm and a torque of 128 Nm, represents an outstanding performance capability, Gerhard Meisl elaborates.
The travel range of the B-axis is 205°. This is continuously adjustable at a resolution of 0.001°. Additionally, the B-axis can be clamped in any orientation and indexed in 5° increments. Also, the main, back and milling spindles, as well as the hydraulic pump, are cooled. „The knee joint, which is made from highstrength aluminum, must be manufactured to a tolerance of +/- 0.005 mm. Due to the outstanding thermal stability of the HT 95, we are able to produce good parts from the get-go – dimensional repeatability is also assured“, Konrad Kainz boasts.
The lower magazine is equipped with 12 live tools. 80 additional tools are located in the integrated tool magazine. „Depending on the customer requirements, the modular machine concept also provides the option for a tail-stock solution in combination with an NC controlled steady-rest, Gerhard Meisl adds.
New LM 1500 LF bar-feeder
Comprehensive automation is provided by the MKE developed LM 1500 F bar-feeder. The benefit of the latest development is that bars can be fed from the front, for instance allowing the machine to be located directly against a wall. „A highly modern industrial machine demands advanced supporting automation.
The LM 1500 F gives us the ability to offer ergonomically efficient loading features for bars up to Ø 95 mm with only a small floorspace“, explains Gerhard Meisl. The finished parts are pushed into the part catcher by the coolant flooded part ejector, and deposited on a conveyor belt.
„With the HT 95 we are able to to produce most complex parts 30 percent faster than before. At large quantities per year, this represents a noticeable saving and/or capacity increase“, Eng. Erwin Poinstingl summarizes.
Using the new Hyperturn 95 SMB from EMCO, MKE automatically produces most complex components from rods on the main and back spindle, 30 percent faster than before.
MKE‘s newly developed LM 1500 F bar-feeder provides for ergonomically efficient loading of bars up to Ø 95 mm at a small footprint.
Metall und Kunststoffwarenerzeugung GmbH, set in the northern woods section of Austria, is steeped in tradition - the company can look back on 100 years of experience and know-how. As early as 1881, the Heidenreichstein based company started making a name for itself by processing metal and leather. These activities then developed into a company specializing in sheet metal and metal processing.
At its peak, the company employed as many as 1,000 staff members, being and was known internationally after the World War 2 for producing high-end cigarette lighters and cases. Since 1989, the company has been operating as a subsidiary of the Haas Group, the largest manufacturer world-wide of systems and machines for waffle, cookie and ice-cream cone production.
„While our production activities have historically focused on high-end cigarette lighters, we have now matured into a full-service provider of metal and plastics processing capabilities. Our broad spectrum of products and services leave no needs unaddressed“ is how MKE‘s Managing Director, Eng. Erwin Poinstingl, describes today‘s activities. Specifically, the currently 190 employees produce paper currency systems, hydrants, fittings, valves, electrohydraulic rail-switch drives, as well as bar-feeder systems for machine tools. The product line is rounded off by complete automation projects for the automobile and food industries, as well as an expansive parts machining capability.
Caption 1:
At MKE, programming tasks are performed with the ESPRIT CAM system, and also directly at the machine using the Sinumerik 840D-sl by Siemens. (note: pictured – Andreas Schramel, CNC Machinist)
Caption 2: The Hyperturn 95 from EMCO allows MKE to significantly increase its capacity for complete machining of complex components.
Caption 3: EMCO machines are generally top-notch with respect to quality and are also priced well. This is complemented by exemplary and reliable service – these are key benefits.
Eng. Erwin Poinstingl,
MKE Managing Director
Caption 4: The HT 95 gives us the ability to produce parts up to 30 percent faster than before. This represents a noticeable saving and/or capacity increase.
Konrad Kainz, Product and Project Manager at MKE
Caption 5: The Hyperturn 95 is equipped with the most up-to-date technology, and ideally designed for machining parts from bar stock up to a diameter of 95 mm. In combination with the new LM 1500 F bar-feeder, this provides for the utmost in productivity and flexibility.
Gerhard Meisl, Product
Management Manager at EMCO
Caption 6: Among others, MKE has specialized in the production of complex medical technology components.
Technical data
HYPERTURN 95
Work area
Swing over bed: 720 mm (28.3")
Distance between spindle noses: 1700 / 2300 mm (66.9 – 90.6")
Max. Bore in Draw Tube: 95 mm (3.7")
Travel
Travel in with milling spindle X1 / Z1: 550 / 1300 – 1900 mm
Travel in 2 / Z2: 300 / 1340 – 1940 mm
Y travel in: 240 mm (+/- 120 mm)
Main and counter spindle (A2-8)
Maximum speed: 3500 rpm
Maximum power: 33 kW (44.3 hp)
Maximum torque: 800 Nm (590 ft/lbs)
Tailstock
Taper mounting (integrated bearing): MT 5
Travel in: 1100 / 1600 mm
Quill stroke: 150 mm (5.9")
Quill diameter: 150 mm (5.9")
Tool turret top and bottom
Number of tool positions: 2 x 12
Tool holding shaft in accordance with VDI (DIN 69880): 40 mm
Driven tools
Speed range: 0 – 3000 rpm
Torque: 40 Nm (29.5 ft/lbs)
Drive performance: 10.5 kW (14 hp)
Driven tools: 2 x 12
B-axis and PowerMill
Travel range : 205°
Tool magazine positions : 40 (80 optional)
Tool holder: HSK63, C6, C5
Maximum torque: 128 Nm (94.4 ft/lbs)
Maximum power: 21.5 kW (28.8 hp)
Maximum speed: 7000 (12000) rpm
Tool change time (tool - tool): 2.2 sec
Feed drives
Rapid motion speed X / Z counter spindle: 30 m/min (1181 ipm)
Rapid traverse speed in Y: 15 m/min (590 ipm)
Coolant system
Tank volume: 420 / 520 liters
Pump capacity: 14 bar / 10 l/min
Dimensions
Height of center above floor: 1360 mm
Overall height: 2800 mm
Space required inclusive tool magazine: 8500 / 9100 x 3150 mm
Total weight: 16000 – 22000 kg
Safety devices: CE compliant
Highlights Hyperturn 95 SMB
- Thermosymmetric, high-performance main and counter spindle design
- Large working area with either two tool turrets or with milling spindle and one tool turret for maximum flexibility
- Direct driven C-axes for high accurate milling and drilling operations
- Integrated, completely covered tool magazine for up to 80 stations
- Rugged machine frame for the utmost in accuracy and production quality
- Optional: CPS Pilot – The virtual HYPERTURN for collision-free programming and optimal machine utilization
About MKE Metall- und Kunststoffwarenerzeugungs GmbH
Metall und Kunststoffwarenerzeugung GmbH, set in the northern woods section of Austria, is steeped in tradition - the company can look back on 100 years of experience and know-how. Today MKE is a full-service provider of metal and plastic processing capabilities.Specifically, the currently 190 employees produce paper currency systems, hydrants, fittings, valves, electrohydraulic rail-switch drives, as well as bar-feeder systems for machine tools.
The product line is rounded off by complete automation projects for the automobile and food industries, as well as an expansive parts machining capability.