www.mexicoindustrial.net
16
'21
Written on Modified on
IMPAQT marca la diferencia
La potencia del software IMPAQT impresiona a los procesadores experimentados.
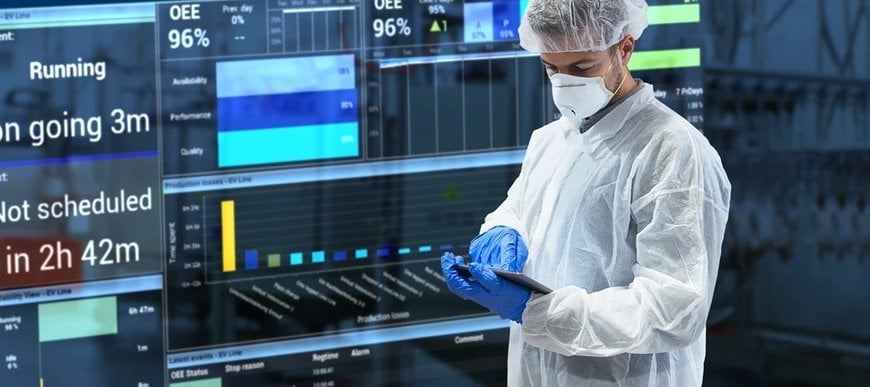
Las posibilidades que ofrece el software IMPAQT son enormes. Los procesadores experimentados encuentran en ella una herramienta extremadamente poderosa que hace realidad cosas que no se atrevían a soñar. Están especialmente contentos de que IMPAQT reduzca su tiempo de inactividad. También están satisfechos de poder adaptar su software IMPAQT a sus propias necesidades y requisitos.
La eficacia total de los equipos (OEE), utilizada en todas las industrias manufactureras para medir la eficiencia, suele dividir la medición del tiempo productivo en disponibilidad, rendimiento y calidad. El 100% de disponibilidad, o tiempo de actividad, significa que un proceso de fabricación está siempre disponible sin paradas imprevistas. El rendimiento del 100%, o productividad, se define comparando el valor máximo teórico con los resultados reales, incluyendo por qué y dónde se han producido pérdidas de rendimiento. El 100% de calidad significa que el proceso de producción no tiene ninguna pérdida de calidad, sin productos de un sola pata, caídos o rechazos veterinarios.
IMPAQT impresiona
IMPAQT ofrece a los procesadores nuevas posibilidades que nunca antes habían tenido. László Bárány, director general de Master Good en Hungría, la mayor empresa de integración de pollos de engorde del país, lo explica así:
“Obviamente estamos interesados en que nuestros equipos den lo mejor de sí en todo momento. Con IMPAQT podemos concentrarnos inmediatamente en los problemas que causan una caída en el rendimiento o la calidad. Nuestros técnicos tienen una herramienta de valor incalculable a su alcance. Pueden hacer su trabajo crucial de manera aún más eficaz”.
László Bárány, director general de Master Good en Hungría
IMPAQT basa sus conclusiones en hechos
Los procesadores están satisfechos con el efecto positivo de IMPAQT en el sentido de que las decisiones ya no tienen que basarse en las corazonadas del personal de la fábrica. Cuando los operadores pueden pensar que han encontrado la causa de un problema, IMPAQT se basa únicamente en los hechos y, en ocasiones, demuestra que están equivocados. Jan Legters, director de la planta de Esbro en Holanda, pone un ejemplo:
“Tuvimos una buena discusión con nuestro operador de evisceración, que tiene treinta años de experiencia, y que se negaba a creer que la unidad 9 del Nuova funcionaba un tanto menos bien como podría, lo que fue recogido por IMPAQT. Estaba convencido de que era pura coincidencia cada vez que la máquina no funcionaba como debía. Finalmente, le pedí que intercambiara las unidades 9 y 10 y solamente entonces, después de haber observado mi sistema, admitió que IMPAQT tenía razón”.
Jan Legters, director de la planta de Esbro en Holanda
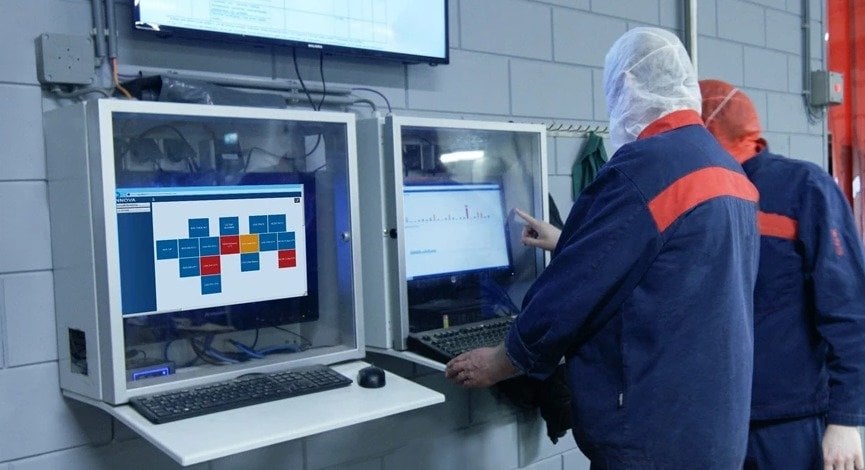
IMPAQT indica las razones
A los procesadores les suele resultar difícil averiguar la causa de una parada de línea. Pero eso ya es cosa del pasado. Están muy satisfechos de que IMPAQT, no solo señale inmediatamente una parada de línea, sino que también muestre el motivo de la misma. Robert Duda, director de aplicaciones y mantenimiento de Cedrob en Polonia, dice:
“IMPAQT nos permite ver exactamente en tiempo real qué eventos se produjeron durante el funcionamiento de la línea. Es mucho más fácil detectar los troles dañados, por ejemplo. Podemos resolver estos problemas mucho antes, lo que realmente minimiza nuestro tiempo de inactividad. En un momento dado, la línea se detuvo, aunque el panel del operador del armario de control no mostraba ningún error. Cada vez que esto ocurría, el personal tenía que esperar a que se reiniciara la línea Revisamos el registro de eventos para ver qué había detenido la línea e IMPAQT señaló la causa inmediatamente. Había un contacto dañado en el interruptor de seguridad. La oxidación estaba causando que las vibraciones de la línea desconectaran el circuito de seguridad cada vez durante un tiempo muy corto. Fue bueno descubrirlo, porque nos ahorró muchos problemas.”
Robert Duda, director de aplicaciones y mantenimiento de Cedrob en Polonia
IMPAQT mejora el proceso
Con IMPAQT, una alerta ya no causa pánico. Por el contrario, si todo el mundo en la fábrica y en la sala de control sabe exactamente lo que tiene que hacer, existe la posibilidad de mejorar aún más el proceso. El motivo exacto de una alarma puede analizarse rápidamente y prevenir futuras alertas. Como resultado, el proceso se optimiza. Jan Legters pone un ejemplo:
“Normalmente, los operadores no registran lo que ocurre durante una parada de línea. Solo quieren que la línea vuelva a funcionar lo antes posible. Ven un pollo atrapado en el eviscerador, lo sacan, reajustan la máquina, y cuando todo parece estar bien, es chopchop, en marcha de nuevo. Pero eso no nos ayuda a mejorar el proceso, solo es reaccionar a las incidencias. Usando IMPAQT, puedo probar que el túnel de refrigeración se detuvo a las 10:22 con el eviscerador siguiendo 12 segundos después. Por lo tanto, un fallo en el túnel de refrigeración causó la parada y tenemos que echar un vistazo allí para mejorar nuestro proceso”.
Jan Legters, director de la planta de Esbro en Holanda
www.marel.com